-
Lithium-ion batteries – electrolytes – solid & semi-solid
-
Upon infusion of positive electrodes with liquid TMA ∙ CFSI (1 mass%, tetramethylammonium 1,1,2,2,3,3-hexafluoropropane-1,3-disulfonimide, anion: see Figure),
cells with sulfide solid electrolyte exhibit an 1 C capacity of 174.4 mAh/g and a capacity retention of 92.0% (1 C charge / discharge), as compared to
88.3 mAh/g and 79.7% for comparative cells that did not undergo a liquid infusion step.
Positive electrode formulation: LiNi0.8Mn0.05Co0.15O2 (NMC) / Li6PS5Cl /
carbon nanotubes (CNT) / polytetrafluoroethylene (PTFE) = 90 : 9.6 : 0.15 : 0.25 by mass.
Negative electrode current collector: carbon black / silver particles / binder (Kureha) = 69 : 23 : 8 by mass.
Solid electrolyte layer: Li6PS5Cl / binder (Kureha) = 99 : 1 by mass, deposited directly on negative electrode current collector
('anode-free' cell design that does not require handling of metallic lithium during production).
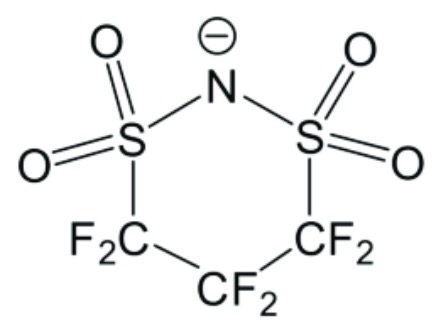
This work illustrates how a very minor quantity of a well-selected ionic liquid (such as cyclic sulfonamide anions)
substantially improves performance in so-called 'anode-free' sulfide cells (specifically upon employing a 1 C charging step during cycling).
An interesting question is if some of the ionic liquid percolates to the negative electrode and forms SEI, which in turn might block
pores through which lithium metal dendrites could otherwise be formed.
In any case, negative effects in terms of potential safety disadvantages or risk of leakage due to the presence of a small amount of ionic liquid
appear minimal, as the ionic liquid presumably exhibits no gas formation upon heating to at least 200°C.
-
The premium version includes another two patent discussions, plus an Excel list with 50-100 commercially relevant recent patent families.
-
Lithium-ion batteries – negative electrode (excluding Li metal electrodes)
-
Conductive additive: Al2O3 particles (average diameter: 20 nm) were coated with carbon through CVD
(chemical vapor deposition, 1,000°C, CH4, 7.5 h) to obtain a graphene-Al2Oz (0 < z < 3) conductive additive
(60 mass% Al2Oz).
Si-carbon composite active material: flake graphite (SFG6, IMERYS), pitch, and silicon were mixed with isopropanol, spray-dried, and carbonized (900°C).
This process yields a silicon-carbon composite active material (D50: 13 μm).
Graphite, Si-carbon composite active material, conductive additive & PTFE (polytetrafluoroethylene) were dry-mixed (83.1 : 14.4 : 0.4 : 2.1 by mass)
in a blade mixer (25°C, 1,200 rpm, 10 min) to form a first dry mixture. This mixture was further mixed (5,000 rpm, 20 min) for
fibrillization (fiberization of PTFE).
The resulting mixture was extruded (50 MPa) to create a self-standing negative electrode film, which was subsequently laminated on a
copper foil pre-coated with a carbon black (Denka) / PTFE intermediate film (1 μm thickness). These electrodes exhibit an adhesion of 6.8 gf/mm.
Half-cells with ethylene carbonate (EC) / ethyl methyl carbonate (EMC) / dimethyl carbonate (DMC, 2 : 4 : 4 by volume) /
vinylene carbonate (VC, 1.5 mass%) / LiPF6 (1.15 M) as electrolyte exhibit a first cycle efficiency of 85.8% and a capacity
retention of 98.9% after 50 cycles (0.2 C charge / discharge).
This work illustrates how Samsung SDI developed a dry negative electrode manufacturing process that enables favorable adhesion
and cycling stability, through employing graphene-Al2Oz (0 < z < 3) conductive additive, and a carbon-coated
Cu current collector foil.
Employing carbon-coated Al2Oz (0 < z < 3) as conductive additive appears to be a breakthrough that facilitates
implementation of dry coating processes, potentially because of improved rheological characteristics as compared to carbon nanotubes / carbon black.
To increase first cycle efficiency, the Si-carbon composite might be replaced with a material that exhibits a lower active material /
electrolyte interface area, or a solid electrolyte / anolyte might be employed that exhibits lower SEI formation reactivity
as compared to liquid carbonate-based electrolytes.
-
The premium version includes another two patent discussions, plus an Excel list with 50-100 commercially relevant recent patent families.
-
Lithium-ion batteries – positive electrode
-
Conductive additive: Al2O3 particles (average diameter: 20 nm) were coated with carbon through CVD
(chemical vapor deposition, 1000°C, CH4, 7.5 h) to obtain a graphene-Al2Oz (0 < z < 3) conductive additive
(60 mass% Al2Oz).
LiNi0.91Co0.05Al0.04O2, the above conductive additive and carbon nanotubes (CNT, 99.75 : 0.2 : 0.05 by mass)
were milled (5-30 min, 1,000-2,000 rpm, Nobilta mixer, Hosokawa).
The resulting material, LiNO3,
succinonitrile, CNT, Ketjen black, and PTFE (polytetrafluoroethylene) were first mixed (95 : 0.5 : 0.5 : 1.4 : 0.6 : 2 by mass, 1,200 rpm, 10 min),
followed by a second mixing step (4,000 rpm, 25 min, blade mixer) to allow for fibrilization (fiberization of PTFE).
The resulting mixture was extruded into a self-standing positive electrode film, which was subsequently roll-pressed (3.5 tons/cm2,
thickness: 150 μm), followed by lamination onto an
Al foil pre-coated with a carbon black (Denka) / PVDF (polyvinylidene difluoride) intermediate film (1 μm thickness).
In half-cells, a capacity retention after 350 cycles of 94.6% was measured (0.1 C charge / discharge),
as compared to 85% for a comparative electrode prepared using a wet process (PVDF binder, no use of graphene-Al2Oz (0 < z < 3)).
Employing carbon-coated Al2Oz (0 < z < 3) as conductive additive along with a minor amount of
succinonitrile (melting point: 58°C, boiling point: 266°C) might be a key breakthrough that could facilitate
industrialization of dry positive electrode coating processes, including the potential avoidance of undesired
temperature increases and/or production equipment damage due to excessive shear-thickening effects.
According to patent filings, succinonitrile is frequently used as an electrolyte additive in semi-solid electrolytes. Its presence in the
electrolyte mixture should not cause performance or safety problems.
-
The premium version includes another two patent discussions, plus an Excel list with 50-100 commercially relevant recent patent families.
-
Fuel cells (PEMFC / SOFC / PAFC / AEMFC) – electrochemically active materials
-
An organic carbon-forming precursor, a zirconium salt doping precursor, and a pore-forming agent were combined to form a precursor mixture.
The mixture was heat-treated (1,300–1,500°C, ≈15 min) to form a zirconium oxide-doped carbon support (particle size: ≈400 nm, ≈1.5 mass%
with respect to carbon support) with
pores (pore diameter: ≈50 nm).
Platinum-based catalyst nanoparticles were dispersed on the zirconium oxide-doped carbon support, followed by a heat-treatment (300–1000°C,
≈2 h) to arrange some of the zirconium-based dopants on the platinum-based catalyst nanoparticles (catalyst particle size: ≈0.5 nm).
The Figure below illustrates improved PEMFC cathode catalyst performance and longevity, as compared to a catalyst on a carbon support that does not contain zirconium.
BOL: beginning of lifetime
EOT: end of test
ECS: carbon support
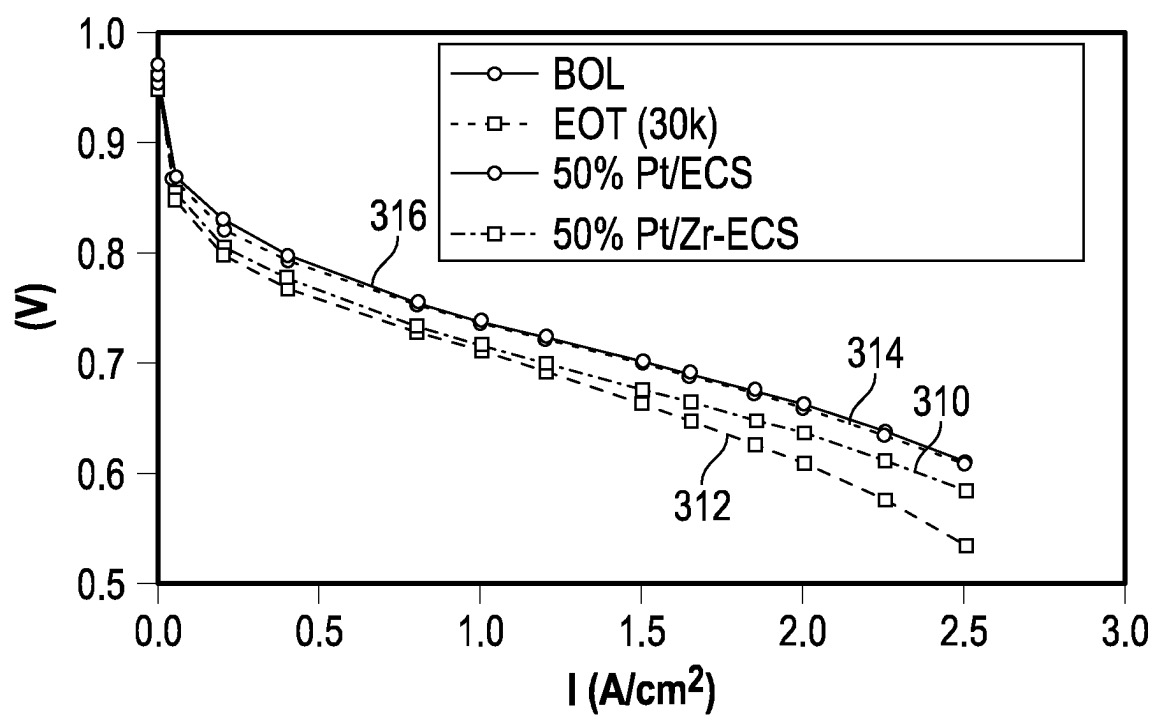
This work illustrates how carbon support doping with zirconium oxide leads to improved PEMFC cathode catalyst performance and longevity.
-
The premium version includes another two patent discussions, plus an Excel list with 50-100 commercially relevant recent patent families.
-
Triweekly patent lists for other categories (Excel files are included for premium users)
-
- Lithium metal containing batteries (excluding Li-S, Li-Air): XLSX
-
- Lithium-ion batteries – electrolytes – liquid: XLSX
-
- Lithium-ion batteries – separators: XLSX
-
- Lithium-sulfur batteries: XLSX
-
- Metal-air batteries: XLSX
-
- Na-ion batteries: XLSX
-
Prior patent updates
-
2024-10-01
-
2024-09-10
-
2024-08-20
-
2024-07-30
-
2024-07-09
|