-
Lithium-ion batteries – electrolytes – solid & semi-solid
-
All solid battery
Applicant:
Toyota Motor /
JP 2024098667 A
TBA-TFSA (TBA: tetrabutylammonium, TFSA: bis(trifluoromethanesulfonyl)amide) and Li-TFSA were mixed and heated (1 : 1 molar ratio). This 'molten salt' mixture
exhibits a melting point of 56°C, as compared to 90°C for TBA-TFSA and 235°C for Li-TFSA.
A slurry in butyl butyrate was prepared with the above salt, Li2S ∙ P2S5 (D50: 0.5 μm) and
PVDF (polyvinylidene difluoride, 94 : 5 : 1 by mass), followed by blade coating on Al foil, drying (100°C, 30 min) and
peeling off to obtain a free-standing layer.
Cells with NCA-based positive electrodes and Si-based negative electrodes were made and tested, along with
comparative cells without 'molten salt' (0.33 C charge / discharge, at 25°C up to cycle 60, then at 60°C).
According to the Figure below, the cells that contain 'molten salt' exhibit a capacity recovery upon heating above
the melting point of the 'molten salt' and comparably slow subsequent capacity losses, as compared to cells without 'molten salt'.
容量: capacity
サイクル: cycle
実施例1: example 1
比較例1: comparative example 1
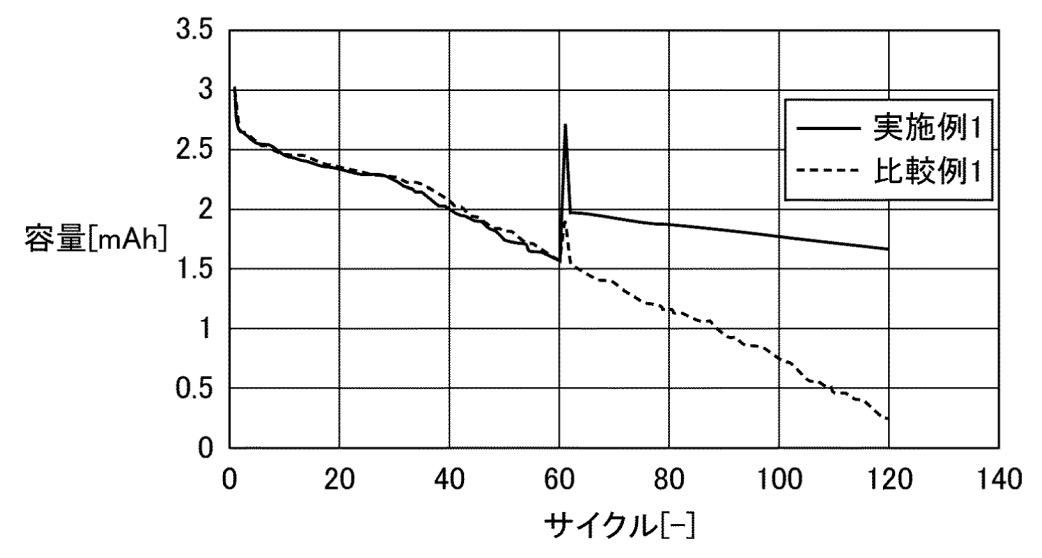
This work illustrates how 'molten salts' can allow for the recovery of capacity upon heating above the melting point,
and how operation above the melting point appears to result in low capacity losses (although it would be interesting
to know cycling behavior after cycling again at 25°C after multiple cycles at 60°C).
The fact that the 'molten salt' is solid at 25°C assures that solid-state cell assembly process steps
can be implemented without having to worry about leakage, while liquid pore infusion manufacturing process steps above 60°C should also be feasible.
-
The premium version includes another two patent discussions, plus an Excel list with 50-100 commercially relevant recent patent families.
-
Lithium-ion batteries – positive electrode
-
Li[Ni1-x-yCoxMny]O2 (0.05 ≤ x + y ≤ 0.15) was dry-mixed
with Co(OH)2 'coating particles' (≤3.5 mol%, particle size: 200 nm), followed by a heat-treatment (≈650°C).
As shown in the SEM images below, the resulting active material particles exhibit a 'diffusion coating layer' with ≈5 nm thickness, while
'coating particles' also remain present at the surface.
In half-cell measurements, a discharge capacity of 209.2 mAh/g was observed, along with an initial resistance of 15.0 Ohm, and
a capacity retention of 93.2% after 50 cycles at high temperature (no further details specified), as compared to
201.2 mAh/g, 17.9 Ohm, and 90.1% for comparative particles without diffusion coating layer.
단입자 양극재: positive active material particle
코팅 입자: coating particle
확산코팅층: diffusion coating layer
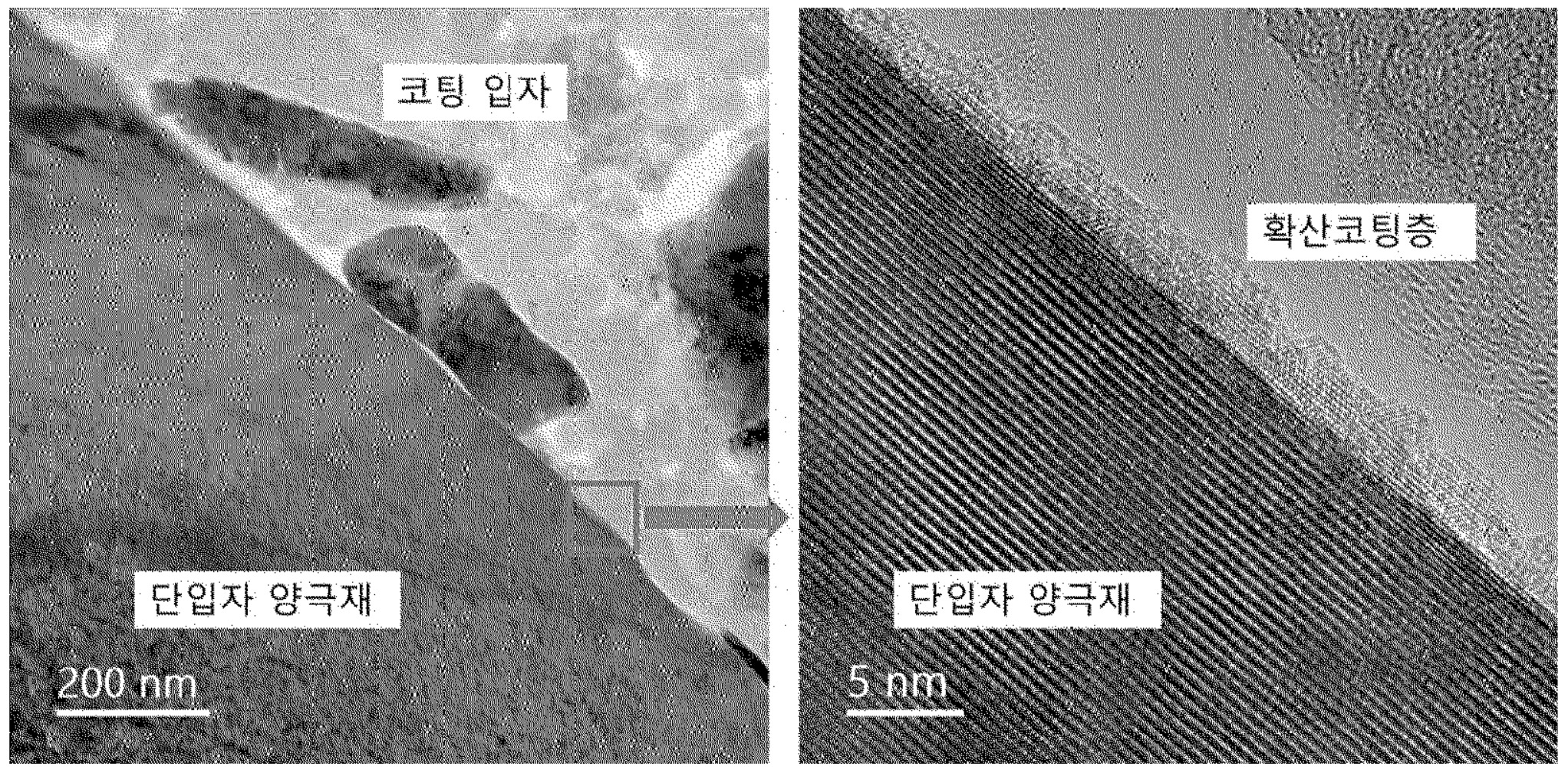
This work suggests that the thickness of the so-called 'diffusion coating layer' on positive electrode materials
can be tailored well upon dry mixing with nanoparticles with the right particle size distribution.
The use of a dry process step could allow for improved process efficiency and reduced waste water quantities. It will be very interesting to see
if other kinds of nanoparticles can be deployed in an analogous manner to vary the composition of the 'diffusion coating layer'.
-
The premium version includes another two patent discussions, plus an Excel list with 50-100 commercially relevant recent patent families.
-
Lithium-ion batteries – negative electrode (excluding Li metal electrodes)
-
As shown in the Figure below, a negative electrode Si-Sn-C active material with very high reversible capacity is described.
Waste tire powder was heat-treated (550°C, 5 h, argon flow, nickel boat), followed by subsequent soaking in sulfuric acid, sodium hydroxide solution, and nitric acid (1 h each, under vacuum),
followed by ultrasonic stirring (30 min), water-rinsing to remove ash and sulfur-containing species, and drying (1 h, under vacuum).
This material was activated in a water vapor device (650°C, 7 h, water vapor to argon flow rate ratio of 1 : 20, nickel boat),
followed by subsequent soaking in sulfuric acid, sodium hydroxide solution, and nitric acid (1 h each, under vacuum),
followed by ultrasonic stirring (30 min), water-rinsing to remove ash, and drying (1 h, under vacuum).
In a separate reaction, silicon powder and tin powder were ball-milled (2 : 1 by mass, 800 rpm), followed by
mixing with magnesium powder (1 : 2 molar ratio) and a heat treatment (600°C, 4 h, under argon) to form a silicon-magnesium-tin alloy.
This alloy, tge waste tire-based activated carbon prepared above, and graphene were ball-milled (750 rpm, 1.5 : 0.1 : 0.08 by mass), followed by
equimolar mixing with SnCl2 and LiCl, and a heat treatment (500°C, 6 h, under Ar). The resulting material
was stirred in 1 M HCl (4 h), followed by filtration, washing with water, and vacuum drying.
The resulting active material exhibits an elemental ratio Si / Sn / C / H / O / N / S = 61.7 : 26.8 : 10.1 : 1.0 : 0.2 : 0.1 : 0.1. In half-cells, the
material exhibits a first discharge capacity of 3,214.7 mAh/g, a first cycle efficiency of ≥94%,
and a capacity retention after 200 cycles of 87% (0.2 C charge / discharge). The Figure below illustrates cycling characteristics at
varying C-rates.
容量: capacity
循环圈数(圈): cycles
充电比容量: specific charge capacity
放电比容量: specific discharge capacity
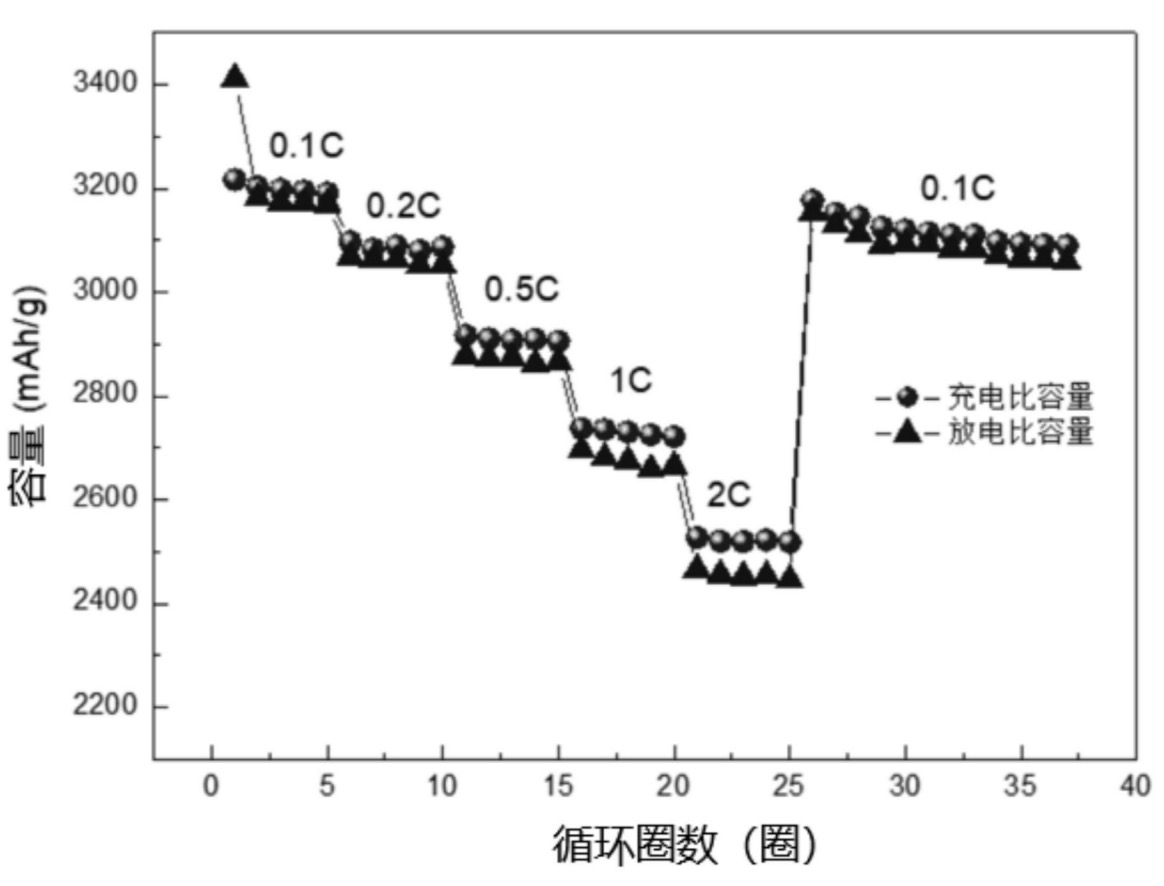
In this patent application, an extraordinarily high capacity along with other excellent cycling characteristics are claimed
by Shanshan as a market-leading player.
Assuming a maximal capacity of 4,200 mAh/g for Si,
and of 994 mAh/g for Sn, a capacity in the
range of ≈2,900-3,000 mAh/g can be calculated without invoking special Li storage mechanisms.
Because the claimed capacity is above this calculated range, it will be very interesting to see a confirmation for these results with more experimental details
(patent applications are not peer-reviewed, while Shanshan
is of course a market-leading, highly accomplished player in this space). Scientific studies on what phenomena drive this extraordinary performance
will be very interesting.
Recycling of used tires into an activated carbon scaffold also constitutes highly relevant work in the context of urgent efforts to improve the energy
efficiency and costs of active material production.
-
The premium version includes another two patent discussions, plus an Excel list with 50-100 commercially relevant recent patent families.
-
Fuel cells (PEMFC / SOFC / PAFC / AEMFC) – electrochemically active materials
-
A Pt precursor (e.g. platinum acetylacetonate) solution in water / acetone or water / ethanol
(adjustment of pH to ≈10.5 with 1 M NaOH)
was mixed with a carbon support material and treated with an electron beam
(≈1 MeV, ≈10 mA, ≈1 min). This procedure resulted in the deposition of Pt nanoparticles.
A Ti precursor (such as TiCl4) was added and the pH was adjusted to ≈7.5 with 1 M NaOH.
This mixture was treated with an electron beam
(≈1 MeV, ≈10 mA, ≈1 min). This procedure resulted in alloying of Ti metal with the Pt nanoparticles (see Figures, Ti / Pt = 5 : 95 by mass).
Upon mixing with Nafion polymer, the catalyst exhibits an electrochemically active surface (ECSA) of 75.4 m2g Pt along with a mass activity
of 0.20 A/g Pt at 0.9 V (measurement in glassy carbon-rotating disk electrode, GC-RDE),
as compared to ≈77.3 m2/g and 0.12 A/g Pt, respectively.
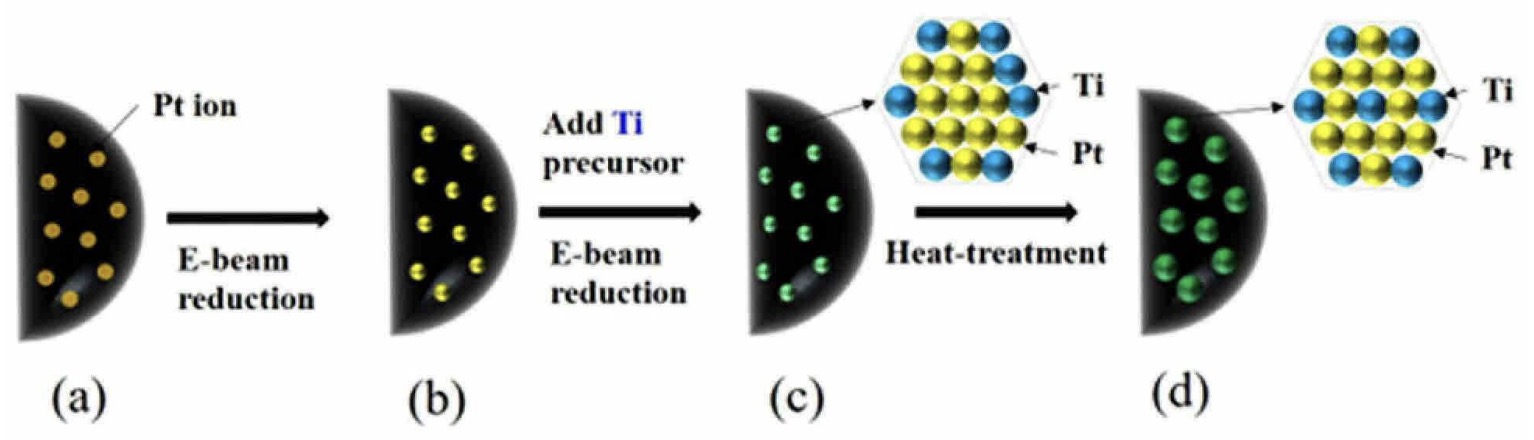
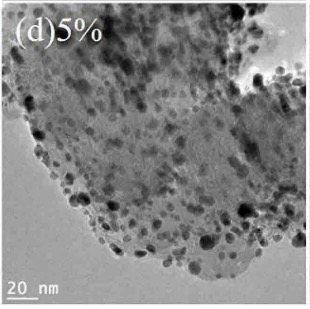
This work illustrates how reduction through electron beam irradiation allows for the formation of well-distributed alloy particles on carbon catalyst support materials.
-
The premium version includes another two patent discussions, plus an Excel list with 50-100 commercially relevant recent patent families.
-
Triweekly patent lists for other categories (Excel files are included for premium users)
-
- Lithium metal containing batteries (excluding Li-S, Li-Air): XLSX
-
- Lithium-ion batteries – electrolytes – liquid: XLSX
-
- Lithium-ion batteries – separators: XLSX
-
- Lithium-sulfur batteries: XLSX
-
- Metal-air batteries: XLSX
-
- Na-ion batteries: XLSX
-
Prior patent updates
-
2024-07-30
-
2024-07-09
-
2024-06-18
-
2024-05-28
-
2024-05-07
|