-
Assessment of Companies
-
Author comments are displayed in maroon.
-
Contemporary Amperex Technology Limited (CATL) – China
-
Organization profile
Contemporary Amperex Technology Limited (CATL, https://www.catl.com/en/) is the world's largest Li-ion battery producer. CATL was founded in 2011 in Ningde, China. In 2017, CATL has completed a split from its parent company ATL/TDK. With BRUNP Recycling (subsidiary), CATL jointly develops positive electrode active materials.
Unique capability: 1) supramolecular ionic liquid / polymer / lithium salt electrolyte membranes with very favorable ionic conductivity (up to 2.4 × 10-3 S/cm) and high boiling point (>438 °C), along with corresponding cells with lithium metal negative electrodes; 2) sulfide electrolyte-based lithium metal cells based on ≥5 complementary concepts to mitigate various failure modes.
Leap of faith: 1) the toxicity of triphenylene-containing electrolytes will be acceptable; 2) the risk of toxic hydrogen sulfide gas emissions when sulfide electrolytes are in contact with water or moisture will not be a showstopper during production, operation and / or recycling.
Comment: approaches 1) and 2) could finally enable the operation of lithium metal negative electrodes at room temperature and below with favorable fast charge / discharge characteristics (along with favorable energy density).
-
News reports & press releases
This information is included in the full version.
-
General patent portfolio characteristics
42 new patent families by CATL related to semi-solid or solid-state Li-ion batteries have been published since 2022
(level 1: 21,
level 2: 24,
level 3A: 8,
level 3B: 1,
level 3C: 11,
level 3D: 9). Polymer / oligomer and sulfide
electrolytes constitute key patenting focus areas (Figure CA-1).
Figure CA-1: AI-based classification of patent families by CATL published since 2022 related to solid electrolytes categories 1-5. Patents without direct relation to one category (e.g. because of solid-state cell packaging focus) were excluded.
-
Key Polymer Electrolyte Product Development Concepts
Figure CA-2: AI-based polymer electrolyte product development concept identification (CATL)
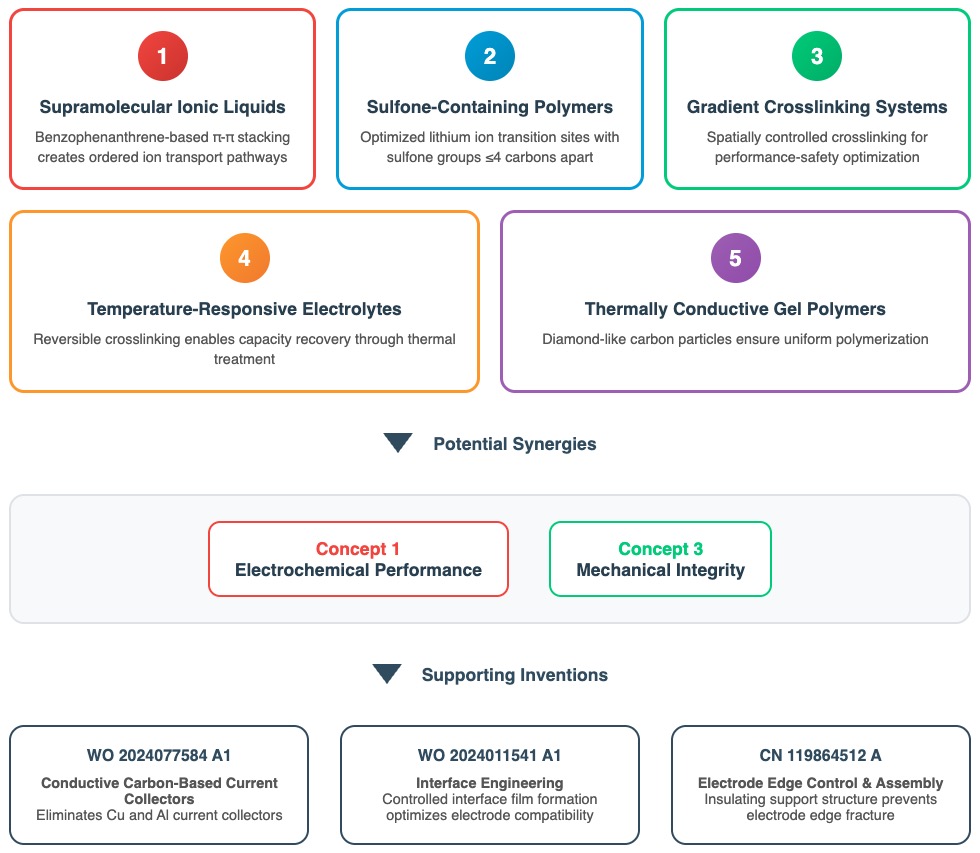
Figure CA-2 illustrates how CATL pursues a range of polymer / oligomer-related product development approaches, among which 2 concepts appear complementary, even though no patent has been identified yet that confirms their simultaneous use.
Concept 1: Supramolecular Ionic Liquids, WO 2022021231 A1 (EPO / Google)
KEY FINDINGS
2.4 × 10-3 S/cm ionic conductivity in membranes based on supramolecular assembly of ion-channels, comparably low density, based on abundant precursors.
TECHNICAL DESCRIPTION
Benzophenanthrene-based supramolecular ionic liquids with π-π stacking creating ordered ion transport pathways. Ether side chains (1-16 carbons, see Figure CA-3) balance molecular assembly with ion mobility. Synthesis via Williamson reaction and FeCl3 cyclization, resulting in 6.5 × 10-3 S/cm bulk conductivity at 25°C.
BACKGROUND INFORMATION
Patent WO 2022021231 A1 addresses the polymer ionic conductivity bottleneck. A self-assembly approach results in near-liquid conductivity (2.4 × 10-3 S/cm in membrane), while offering safety advantages for which solid-state Li-ion batteries are known (triphenylene shown in Figure CA-3 exhibits a boiling point of 438°C). Manufacturing is based on organic chemistry and comparably abundant precursors.
ELECTRODE CONFIGURATION
Negative electrode: lithium metal | Positive electrode: NMC811.
Figure CA-3: top – two triphenylene derivatives with (optionally fluorinated) ethylene oxide / lithium sulfonate groups. The derivative on the left exhibits particularly favorable ion conductivity (6.5 × 10-3 S/cm), while the derivative on the right exhibits particularly favorable cycling stability, bottom – synthesis procedure, OR3 = R1, OR4 = R2 (CATL)
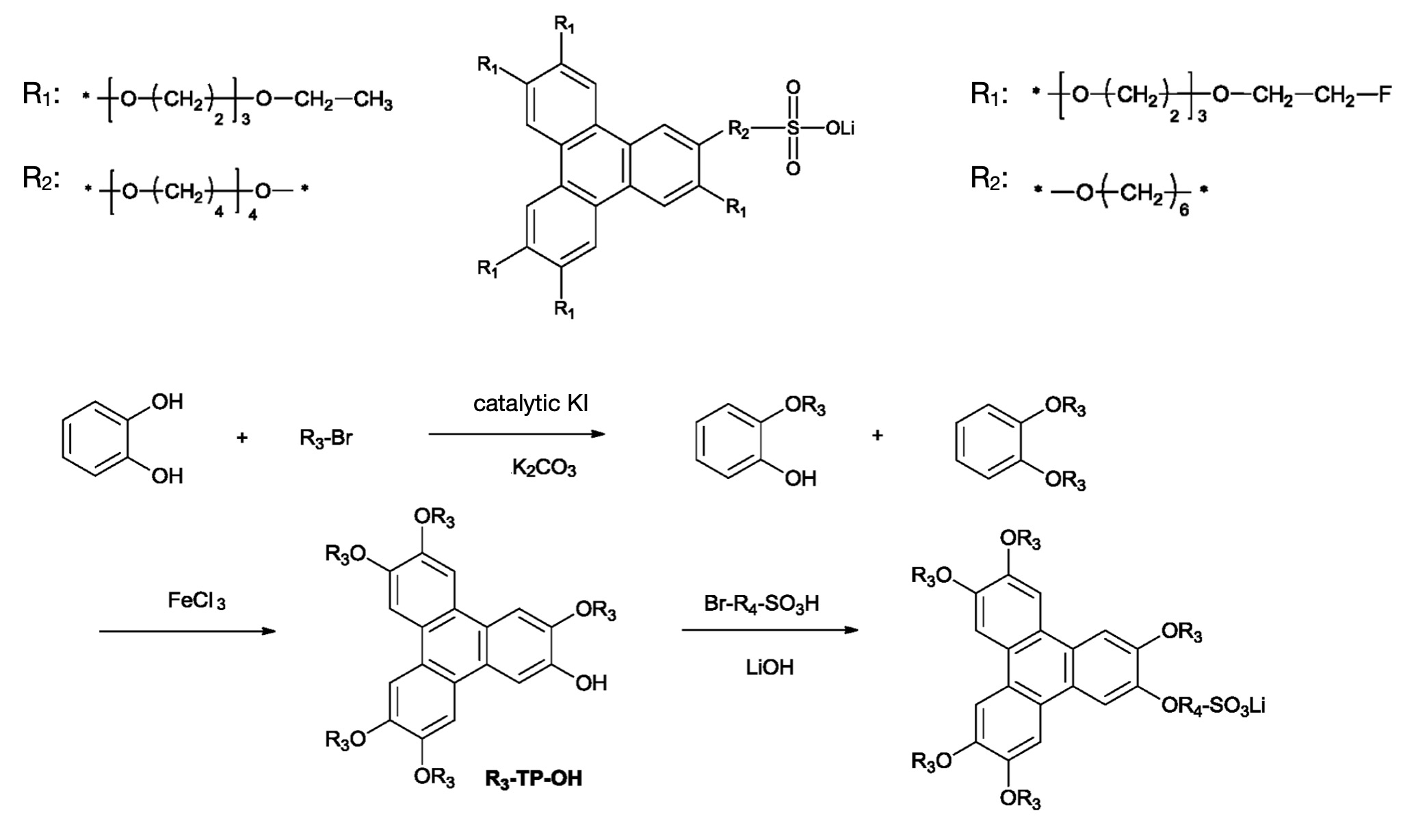
The full version includes a discussion of polymer electrolyte product development concepts 2-5.
-
Potential Synergies Between Concepts
R&D concepts 1 (supramolecular ionic liquids) and 3 (gradient crosslinking systems) offer synergies in terms of overcoming the fundamental trade-offs in solid-state battery development. Concept 1 addresses the critical ionic conductivity bottleneck that has limited solid-state batteries, achieving near-liquid ionic transport through self-assembled molecular architectures. Concept 3 solves mechanical integrity and safety challenges by providing spatially optimized structural reinforcement. The combination could enable solid-state batteries that achieve both liquid-like ionic conductivity and superior structural integrity – previously mutually exclusive characteristics.
-
Possible Material / Cell / Process Characteristics (Projection Based on Public Information)
- Electrolyte: benzophenanthrene-based supramolecular ionic liquids with π-π stacking architecture and ether side chains (1-16 carbons) that exhibit an ionic conductivity of 6.5 × 10-3 S/cm at 25°C (WO 2022021231 A1, Example 22). When integrated with a polymer matrix (PEO/PVDF/LiTFSI at 10-80 : 100 : 5-40 by mass), the composite electrolyte exhibits 2.4 × 10-3 S/cm conductivity. Gradient acrylate crosslinking systems (WO 2024243875 A1) might be incorporated into side chains to tune mechanical characteristics.
- Negative electrode: lithium metal on copper foil (WO 2022021231 A1).
- Positive electrode: NMC811 with conductive carbon (2 mass%) and PVDF binder (2 mass%) on aluminum current collector (WO 2022021231 A1).
- Design: prismatic stacked multilayer cells with favorable deformation resistance (WO 2024243875 A1).
-
Process:
- Supramolecular ionic liquid synthesis via Williamson reaction and FeCl3 cyclization (WO 2022021231 A1).
- Sequential or parallel (such as with multi-slurry feeder) injection gradient crosslinking film formation (WO 2024243875 A1).
- Hot pressing (1-20 MPa, 50-100°C) with spatially controlled crosslinking density.
- Vacuum annealing (60-80°C, 1-8 h).
- Electrode and electrolyte layer lamination through cold-pressing (250 MPa, 25 °C, 2 min) to obtain multi-layer cells.
- Prismatic cell encapsulation.
Supporting inventions listed in Figure CA-2 (bottom) might additionally be employed in this context.
-
Key Sulfide Electrolyte Product Development Concepts
This information is included in the full version.
-
The full version includes a summary and discussion
of 3 additional highly relevant all-solid / semi-solid Li-ion battery electrolyte patents that
have been identified during our triweekly patent screening process.
-
AI-based Patent Summaries
The adjacent Excel file contains AI-based patent summaries for all patents mentioned in this chapter, classified in terms
of electrolyte type (Figure CA-1) and
level 1
(electrode / electrolyte patents) to
level 3D (manufacturing patents).
|