-
Lithium-ion batteries – electrolytes – solid & semi-solid
-
The cage-type polysilsesquioxane / polyethylene oxide hybrid structure shown in the Figure below
was formed through 'click chemistry'
(reaction between azide and alkyne precursors, R1-R6 groups are identical to the siloxane unit
on the top right, m = 6, n = 111).
This structure was mixed with LiN(SO2CF3)2 (LiTFSI, 65 mass%) in tetrahydrofuran, followed
by dripping into a mould and vacuum drying (60°C, 12 h) to obtain a solid electrolyte membrane (thickness: 246 μm)
with an ionic conductivity of 1.8 × 10-2 S/cm. Under a stress of
3.0 MPa, the membrane breaks at an elongation of 94%, and electrochemical stability up to 5.3 V vs. Li+/Li is claimed.
According to
SAXS (small-angle X-ray scattering) spectroscopy, a lamellar phase was formed that is crucial to these favorable performance metrics.
Cells with LFP-based positive electrodes and lithium metal negative electrodes exhibit rate-dependent charge / discharge characteristics as plotted
below
(structure with n = 134, ionic conductivity: 1.2 × 10-2 S/cm). The bottom Figure shows a cycling stability diagram
for 3 different derivatives (实施例1: n = 43, 实施例2: n = 89, 实施例3: n = 134).
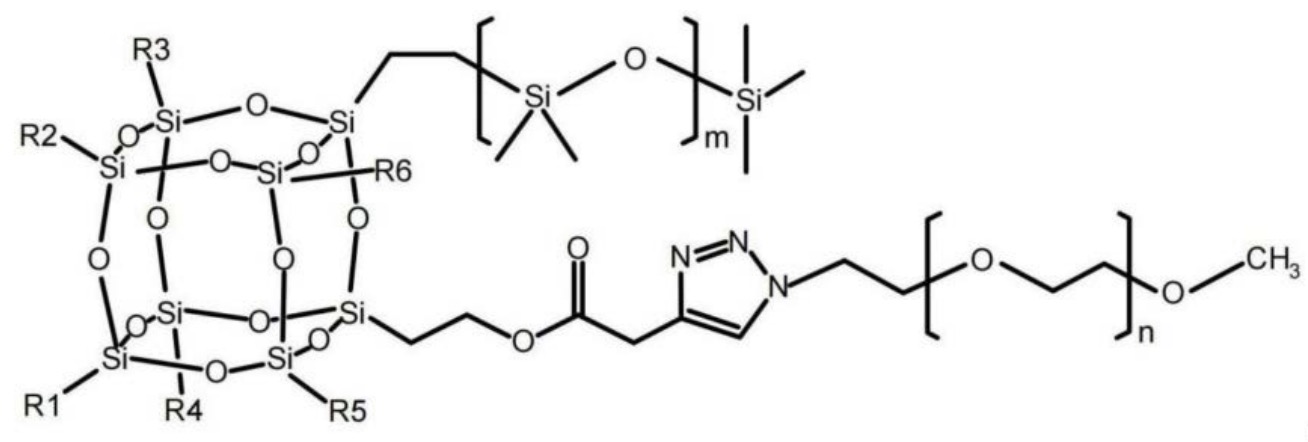
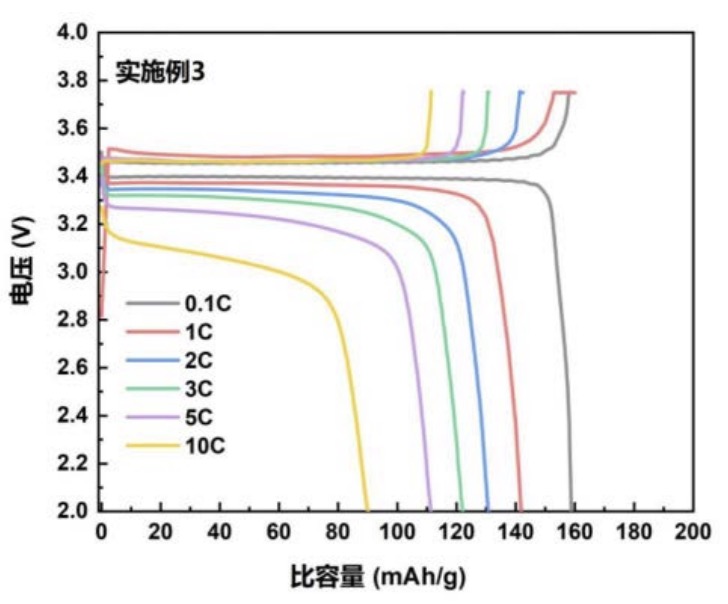
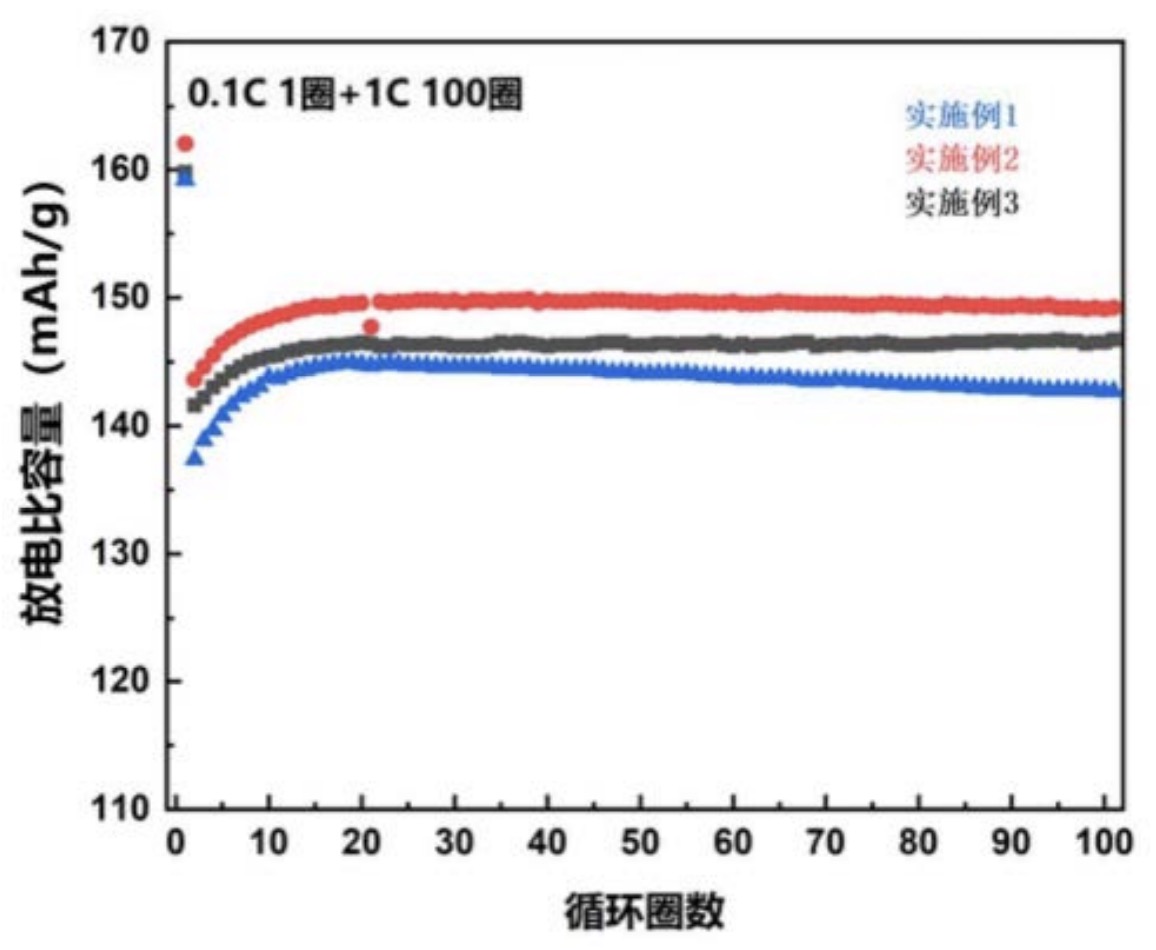
This work illustrates how a supramolecular molecule that forms a repeating lamellar structure enables the formation of a solid electrolyte
film with outstanding ionic conductivity, along with mechanical and electrochemical stability.
It appears that the ethylene oxide groups are protected from oxidation as a result of being incorporated into the supramolecular structure (some
ethylene oxide decomposition might occur at the direct interface to the positive and negative electrodes that
does not seem to cause a detrimental effect on electrochemical performance).
It will be very interesting to watch further up-scaling and commercialization efforts, including if a thinner electrolyte film
can be made and if it is possible to directly coat an electrolyte film onto electrodes.
-
The premium version includes another two patent discussions, plus an Excel list with 50-100 commercially relevant recent patent families.
-
Lithium-ion batteries – positive electrode
-
Lithium carbonate, ferrous oxalate, manganese carbonate, and phosphoric acid
(molar ratio Li / Fe / Mn / P = 1 : 0.35 : 0.65 : 1) were ball-milled in water (2,000 rpm, 80 min),
followed by an aging step (60°C, 1 h).
Glucose (18 mass%) was added to the slurry, followed by stirring, spray-drying and a heat-treatment
(700°C, 10 h).
The resulting material was coarsely ground, sieved and air-crushed to obtain the rod-like, carbon-coated LiMn0.65Fe0.35PO4 (LMFP)
active material shown in the Figure below (BET specific surface area: 18.0 m2/g, 0.1 C discharge capacity: 154.6 mAh/g).
In full cells (graphite-based negative electrodes), the material exhibits a capacity retention of 96.8% after 500 cycles (0.1 C charge / discharge).
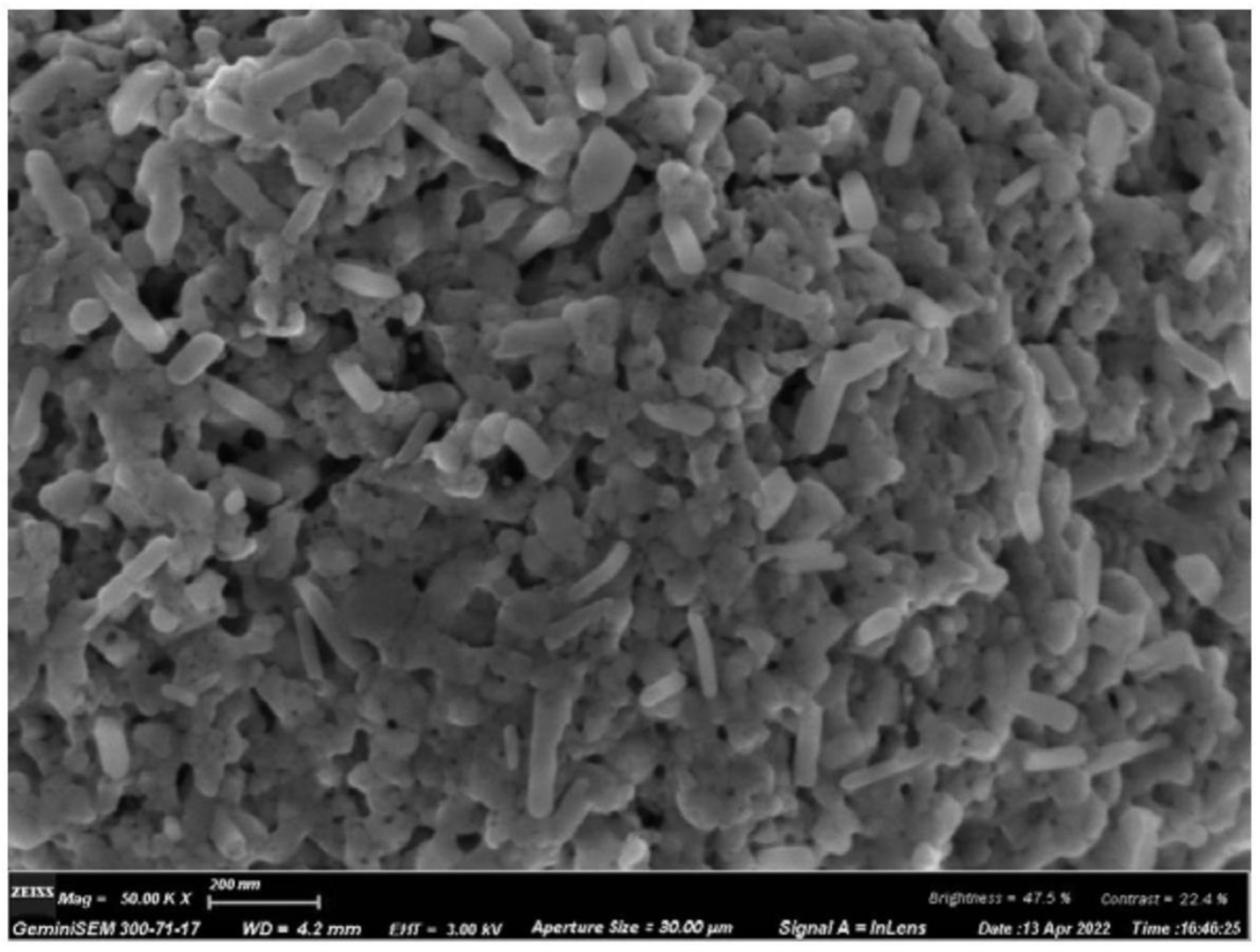
This work illustrates that anisotropic, rod-shaped LMFP particles can be prepared as a result of an aging step at 60°C.
These rods exhibit favorable
cycling stability.
-
The premium version includes another two patent discussions, plus an Excel list with 50-100 commercially relevant recent patent families.
-
Lithium-ion batteries – negative electrode (excluding Li metal electrodes)
-
Cuboid Si-carbon composite active materials were prepared as shown in the SEM images below (top: Si-carbon material powder, bottom: Si-carbon / graphite-based
electrode cross-section).
Negative electrode types A (≈600 mAh/g capacity) and B (≈1,000 mAh/g capacity) were prepared upon mixing with graphite, polyacrylic acid (PAA, ≈4 mass%)
and single-walled carbon nanotubes (SWCNT, 0.05 mass%).
While details for the whole manufacturing process were not identified, a detailed analysis of the impact of ball milling as compared to jet
milling is included as shown in the graph below, which illustrates that jet milling results in a more narrow particle size distribution.
Extensive comparative pouch cell cycling stability data illustrates that an Si-carbon composite material with a narrow particle size distribution
and a BET specific surface area of 3.7 m2/g exhibits the highest cycle life (2,276 cycles until 80% capacity retention,
NMC811-based positive electrodes, negative electrode areal capacity: ≈4.1 mAh/cm2, 2 C charge to 4.0 V, then 1 C charge to 4.2 V,
then 0.05 C charge, 1 C discharge).
SPAN: (D90 - D10) / D50
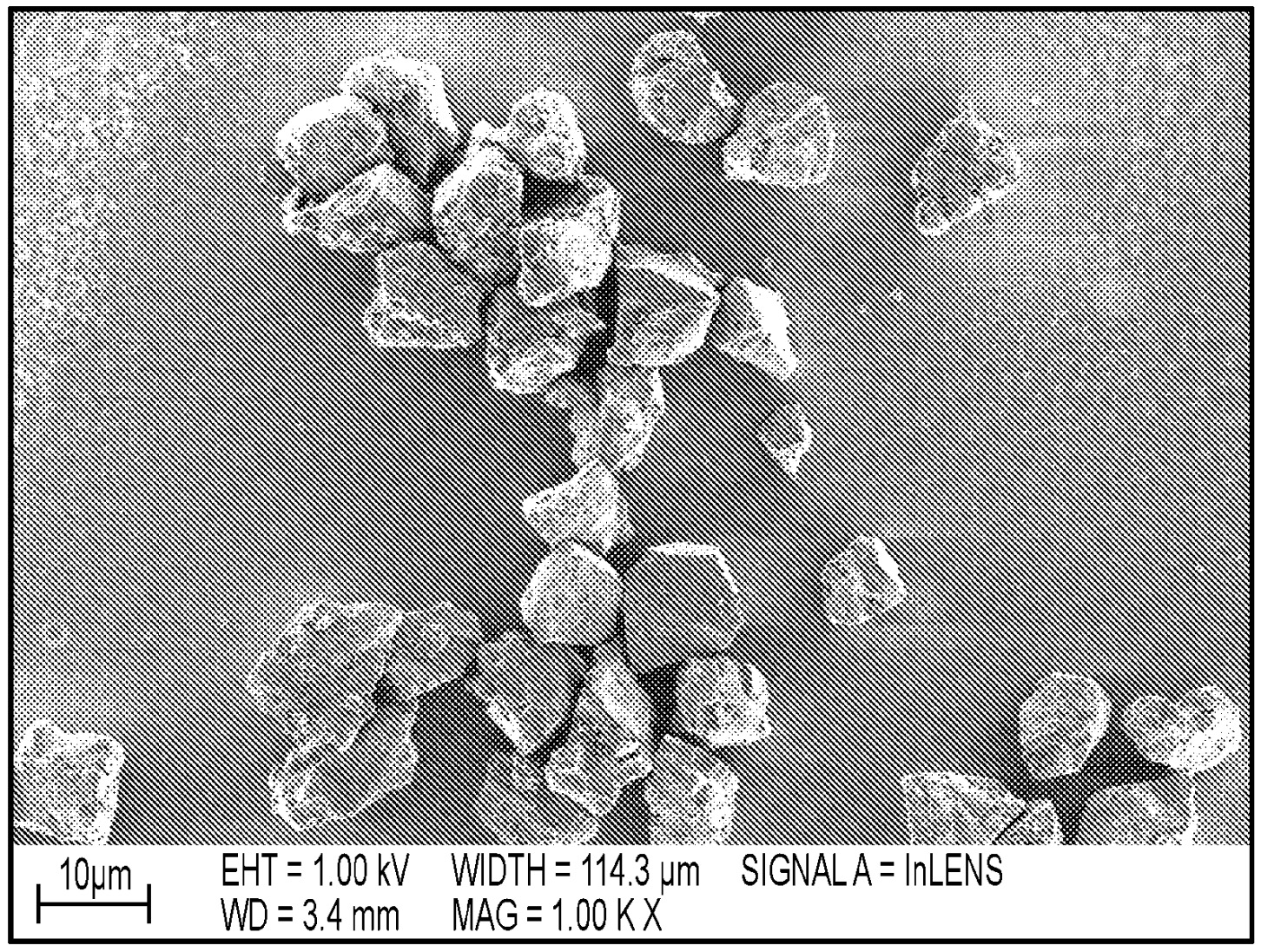
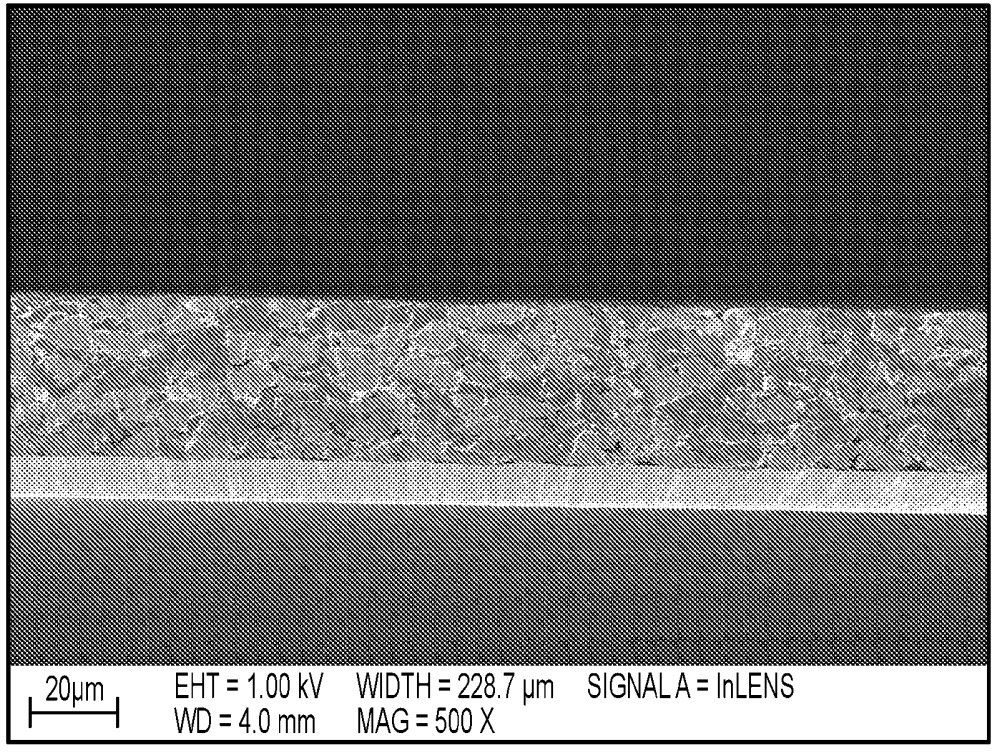
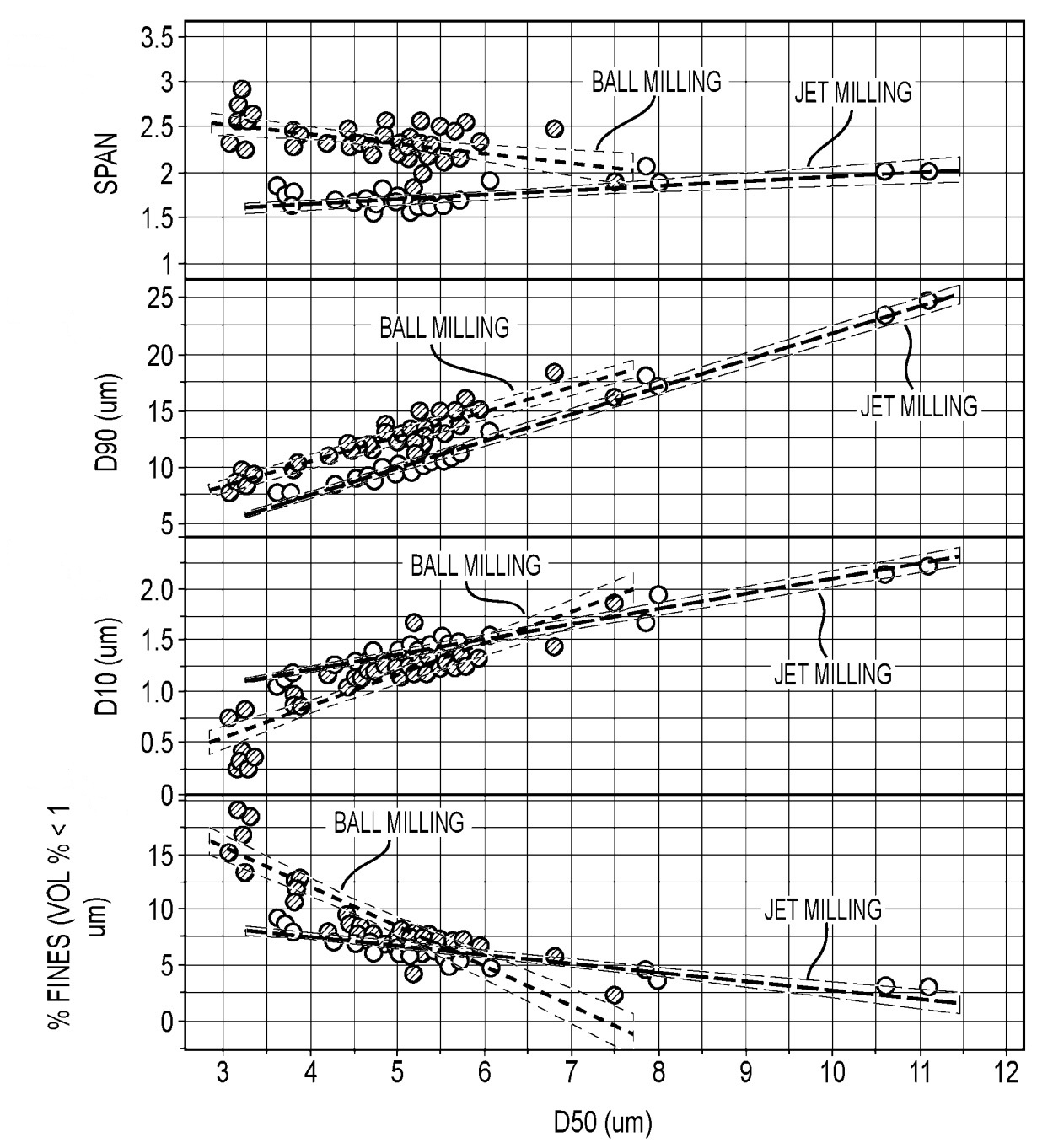
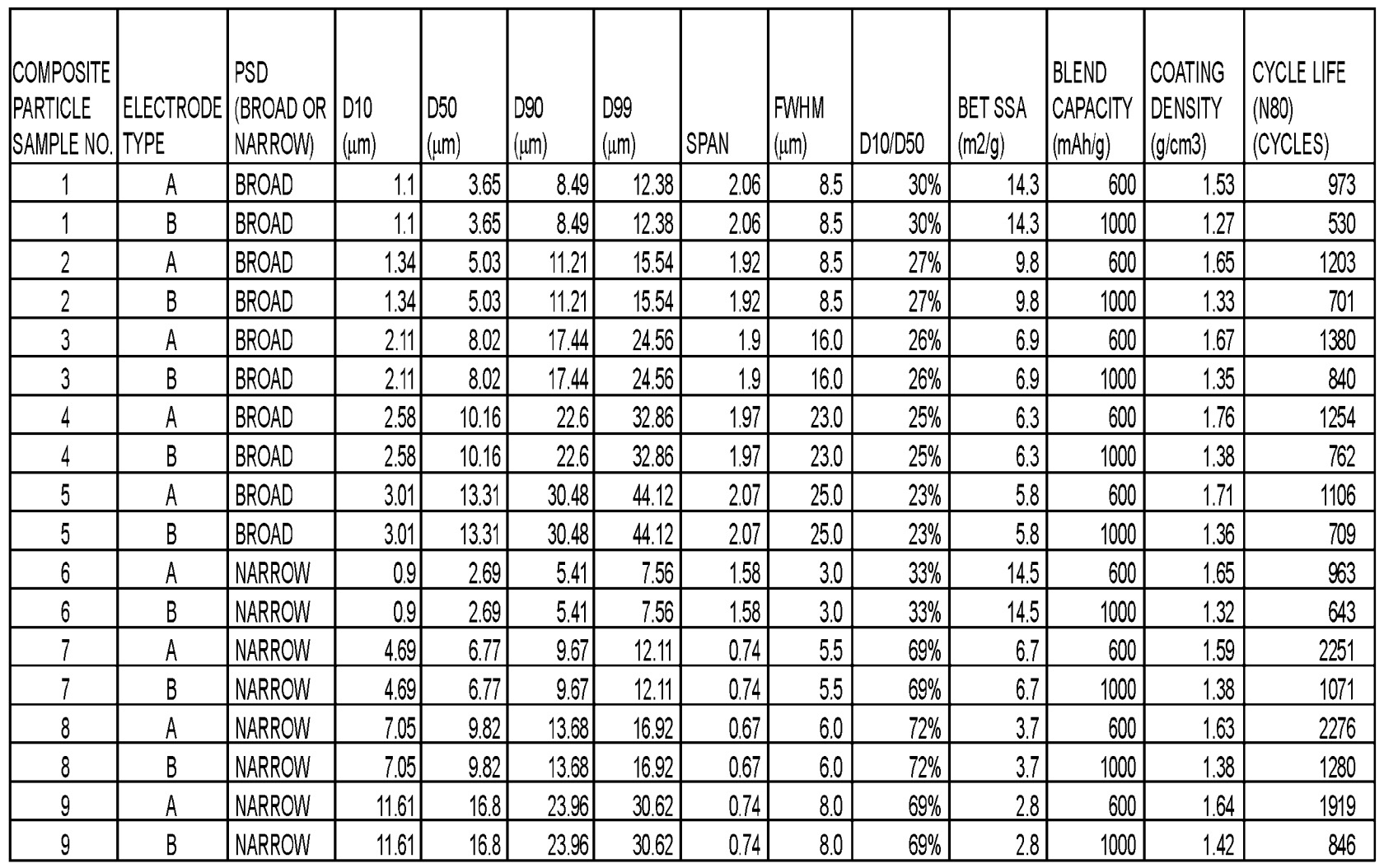
This work tends to suggest that Sila Nanotechnologies shifted its focus from spherical to cuboid Si-carbon composite particles with narrow particle size
and a BET specific surface area of ≈3.7 m2/g, presumably
obtained through jet milling prior to applying the carbon coating.
Presumably, improved longevity was obtained because cuboid particles less easily lose particle-particle contact upon volume expansion (face-to-face
contact by cuboid particles as opposed to point-to-point contact between spherical particles).
In addition, high volumetric energy densities can
also be achieved with cuboid active material particles (less void space as compared to spherical particles with narrow particle size distribution).
-
The premium version includes another two patent discussions, plus an Excel list with 50-100 commercially relevant recent patent families.
-
Fuel cells (PEMFC / SOFC / PAFC / AEMFC) – electrochemically active materials
-
30 mass% Pt / Vulcan (TEC10V30E) was washed with water (100°C) and dried, followed by dispersion in water / 2-propanol.
A polymelamine (PME) solution was added, followed by stirring (room temperature, 3 h), suction filtration and vacuum
drying (100°C, 2 h).
In a pH-controlled, aqueous solution (pH = 8.5, Tris-HCl buffer), the material and dopamine hydrochloride were ultrasonically dispersed
(room temperature, 6 h), followed by filtration and vacuum drying (100°C).
This caused the dopamine to polymerize into polydopamine (PDA).
The powder was heat-treated in a circular furnace (700°C, 2 h, Ar) to carbonize the PME and PDA, followed by washing with water (100°C)
to obtain a carbon-coated electrode catalyst.
A PEMFC cathode catalyst layer was built with Nafion ionomer, which was applied onto a PTFE sheet alongside a
60 mass% Pt/Ketjen-based negative electrode catalyst layer.
The Figures below illustrate that the carbon coating with ≈6 nm thickness leads to a significantly increased mass activity (top),
while the carbon coating with ≈10 nm thickness leads to a substantially improved mass activitiy maintenance rate
(durability test: 10,000 cycles, cycling between 0.6 V and 1.0 V, hold for 3 s at each voltage step).
質量活性: mass activity
炭素膜の厚さ: carbon film thickness
質量活性維持率: mass activity maintenance rate
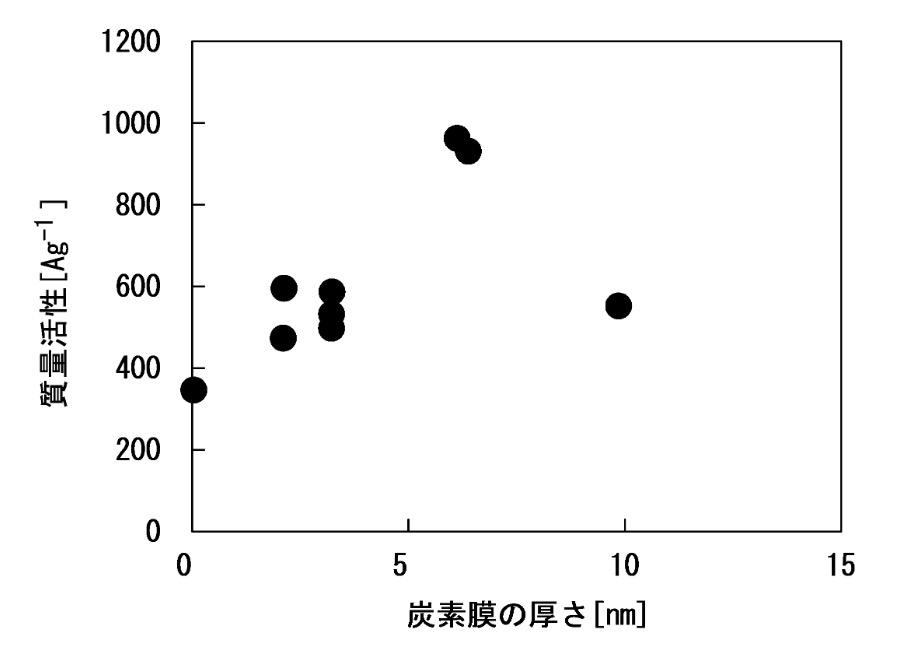
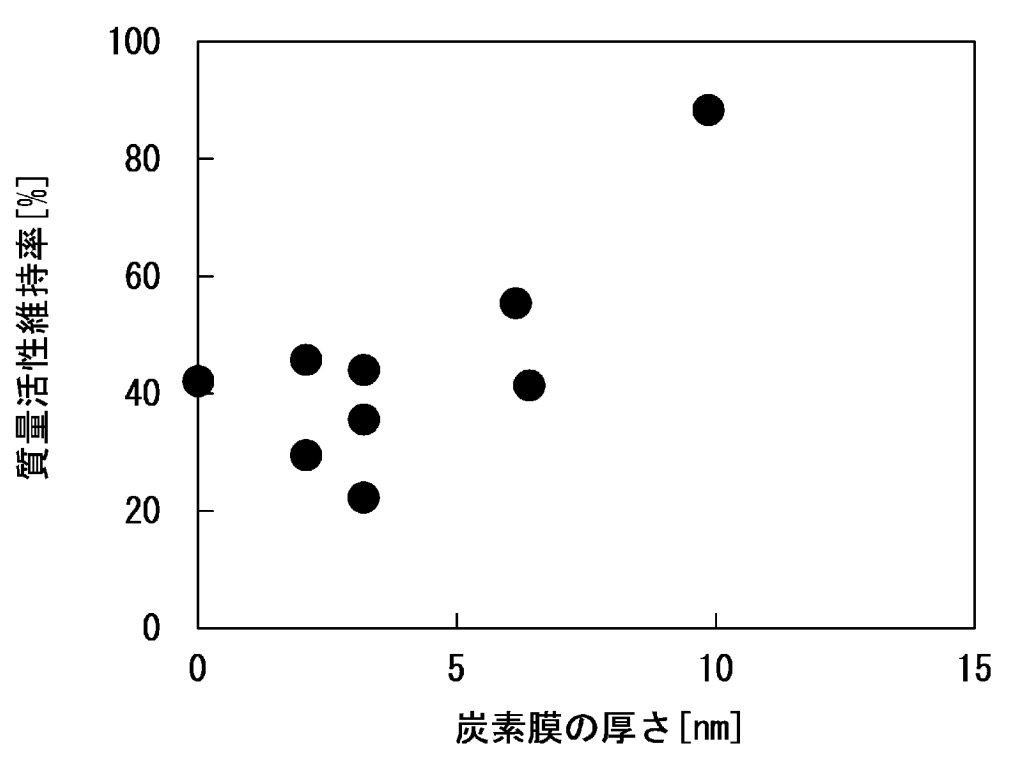
This work illustrates how a carbon coating on the PEMFC cathode catalyst can improve mass activity and maintenance rate,
but it appears that it is hard to balance these two characteristics.
-
The premium version includes another two patent discussions, plus an Excel list with 50-100 commercially relevant recent patent families.
-
Triweekly patent lists for other categories (Excel files are included for premium users)
-
- Lithium metal containing batteries (excluding Li-S, Li-Air): XLSX
-
- Lithium-ion batteries – electrolytes – liquid: XLSX
-
- Lithium-ion batteries – separators: XLSX
-
- Lithium-sulfur batteries: XLSX
-
- Metal-air batteries: XLSX
-
- Na-ion batteries: XLSX
-
Prior patent updates
-
2024-07-09
-
2024-06-18
-
2024-05-28
-
2024-05-07
-
2024-04-16
|